About Norton Packaging
For over 110 years, Norton Packaging has provided precision performance. Whether it’s a rigid plastic pail, a paint can, or a custom package specially designed and constructed, everything we make is crafted to our clients’ exacting standards. And everything we do is built upon our unwavering commitment to their satisfaction.
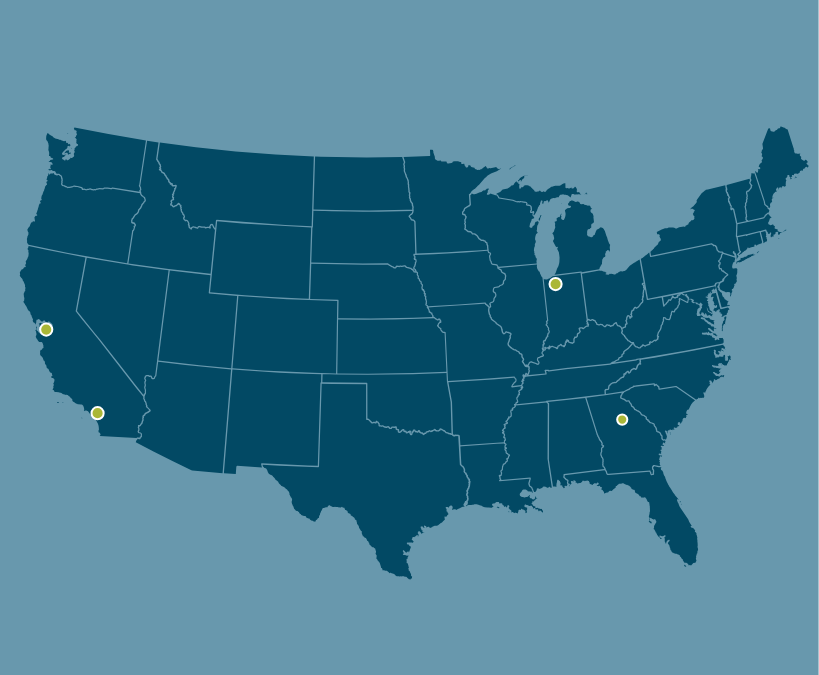
Locations
From our Hayward, California, headquarters, we serve more than 600 customers worldwide. Our three state-of-the-art production facilities located in Los Angeles, CA, Hamlet, IN, and Monticello, GA use the industry’s most advanced equipment and systems—ensuring standardized design and consistency across every mold—to meet the demands of today’s high-speed automated lines.
Our national network has been strategically designed to provide you with a dual advantage. First, our large manufacturing and distribution footprint gives us access to a wider range of suppliers and partners – which keeps costs down and ensures more reliable sourcing. Second, because we’re literally just hours from anywhere, we’re always on the spot with local, personal service.
Our History
Norton Packaging’s history dates back to 1901. That same year oil was discovered in Texas, The Chicago White Sox beat the Cleveland Blues 8 to 2 in the very first American League baseball game, and to the relief of men everywhere, Gillette introduces the disposable razor. It’s safe to say the world has changed since then. But one thing hasn’t; out commitment to constant improvement and unsurpassed customer satisfaction.
1901
Bernard W. Norton establishes a small custom tool shop in Oakland, California, making custom-stamped metal parts for local industries.
1910
The company begins to serve the many small automobile manufacturers springing up along the West Coast. It would soon make parts for the first gyrocopters and mass-produced metal street signs.
1920
Norton Packaging is commissioned to manufacture license plates for the western United States and some of the Pacific Islands.
1939
Howard C. Norton (Bernard’s son) transitions the company from its original product lines into the mass production of steel pails.
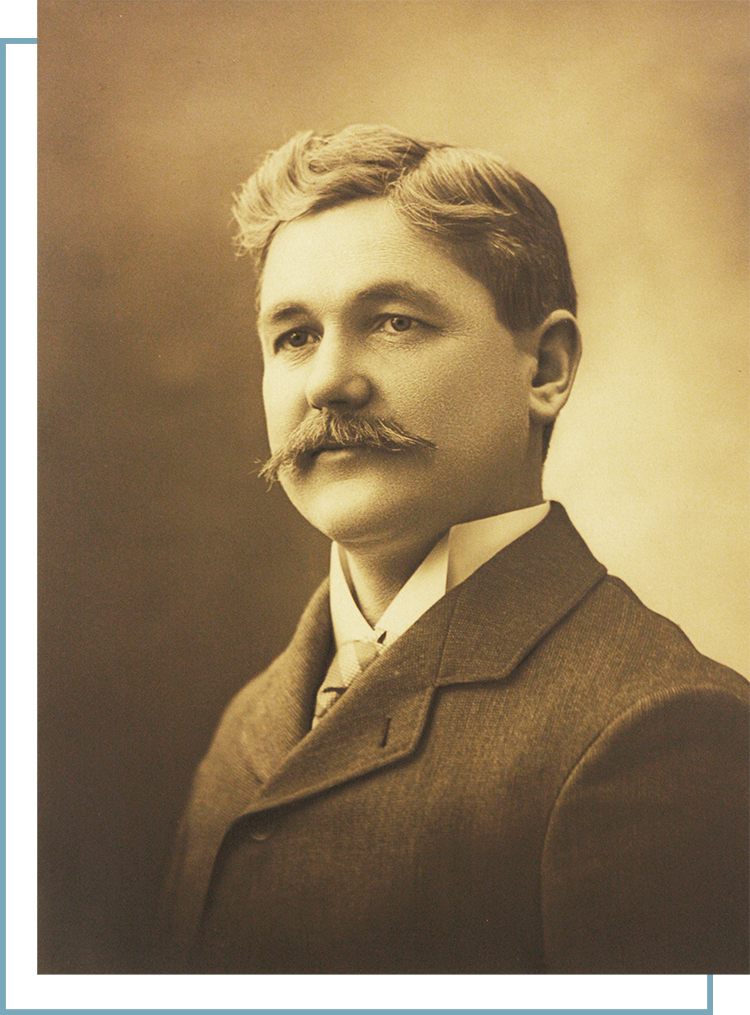
1961
In order to better serve Southern California and the southwestern United States, Norton opens a sales office and a warehouse in the greater Los Angeles area.
1974
The third generation of the Norton family expands the business by purchasing an injection molding machine to produce plastic pails.
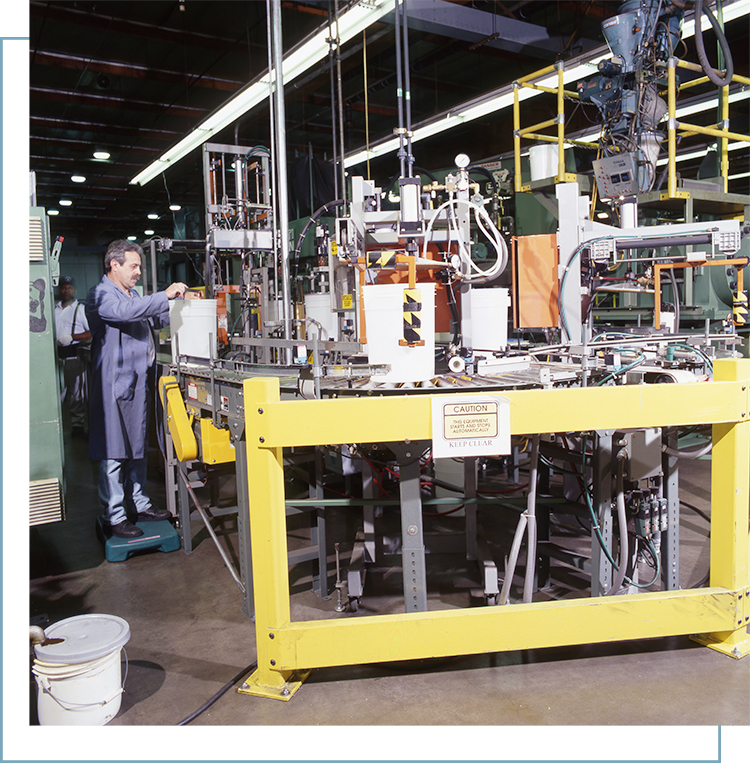
1985
Norton Packaging becomes one of the nation’s leading suppliers of containers – adding product lines, expanding into new markets, and investing in state-of-the-art equipment. Norton exports to the People’s Republic of China and Southwest Asia, including Singapore and Vietnam.
1995
Growing to meet its customer needs, Norton Packaging establishes a distribution center in Hamlet, Indiana, and begins producing pails there just one year later.

2003
Norton Packaging opens a new production/administration facility in its Los Angeles location 102 years after the company’s founding.
2013
Norton Packaging operates two state-of-the-art plants in Los Angeles, California, and Hamlet, Indiana. In addition the company broke ground on a third best-in-class facility in Monticello, Georgia, to serve its customers throughout the southeastern US as well as in Puerto Rico and Europe.
2019
Today, Norton Packaging operates three best-in-class facilities allowing us to serve our customers throughout the US and globally.
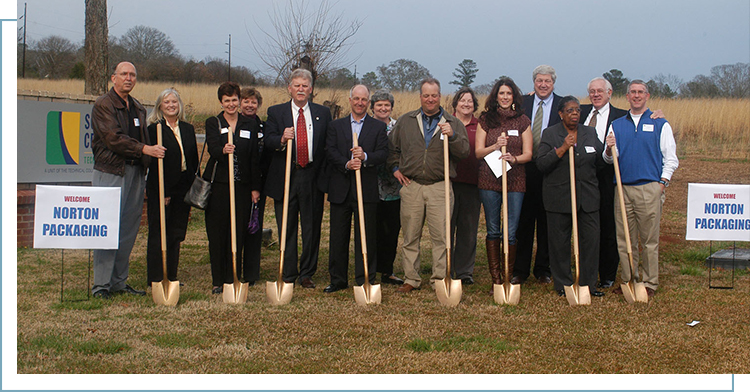
Leadership
Scott Norton
Co-President
Greg Norton
Co-President
Mark Norton
Vice President
JOE SCHRICK
Plant Manager, CA
Jim Koch
Plant Manager, IN
Tom Kenny
Quality Control Manager, IN
Eddie Arzola
Quality Control Manager, CA
Justin Carlino
Director of Sales
Katie Perez
Regional Territory Manager
Rodney Friensehner
Quality Control Manager, GA
Sustainability
Responsible, sustainable sourcing and manufacturing are more than the right way to work. They’re the right thing to do.
We’re leading the way with such innovations as lighter pails that use fewer source materials while maintaining the necessary strength and durability. Many of our smaller pails are manufactured using 25% post-consumer resins. And we’re actively involved in the effort to create pails that can be safely and cost-effectively recycled—preserving natural resources, reducing landfill, and preventing harmful environmental impact.
Our Georgia manufacturing facility will replace power-hungry hydraulic equipment with clean-running, all-electric machinery. Additionally, we’ve strategically located many of our plants near rail hubs to take advantage of cleaner rail transport…thus reducing fuel consumption and greenhouse gas emissions.